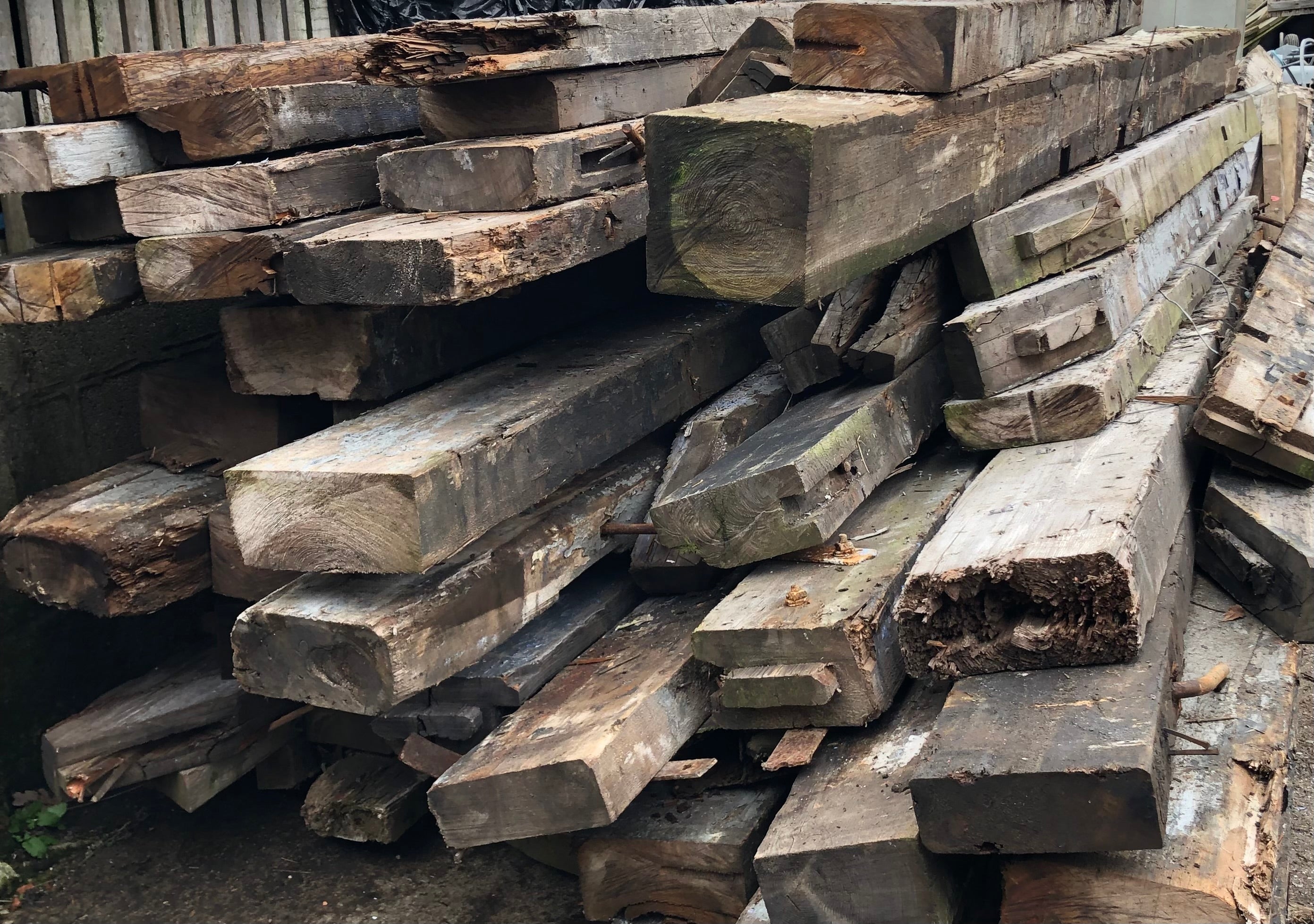
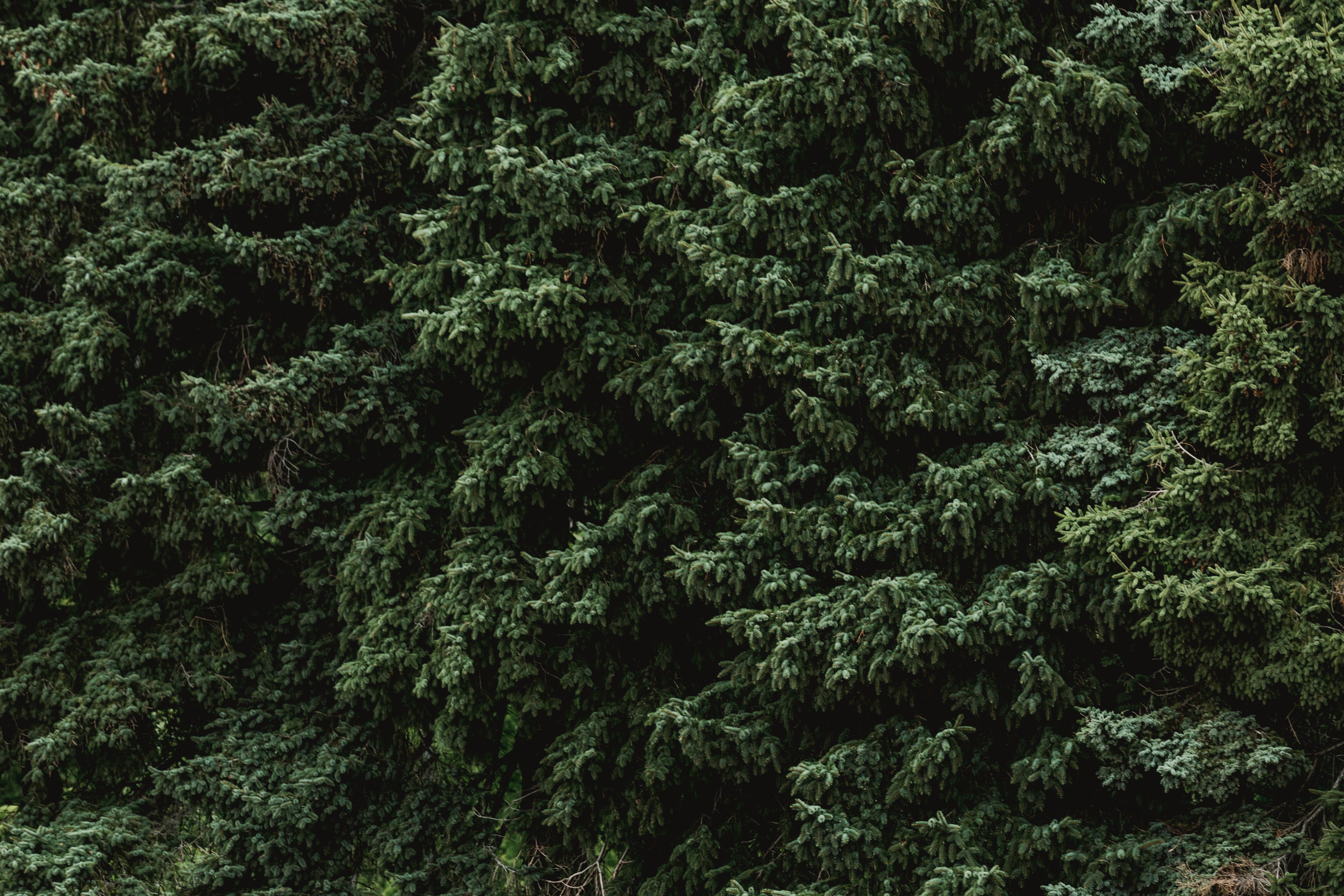
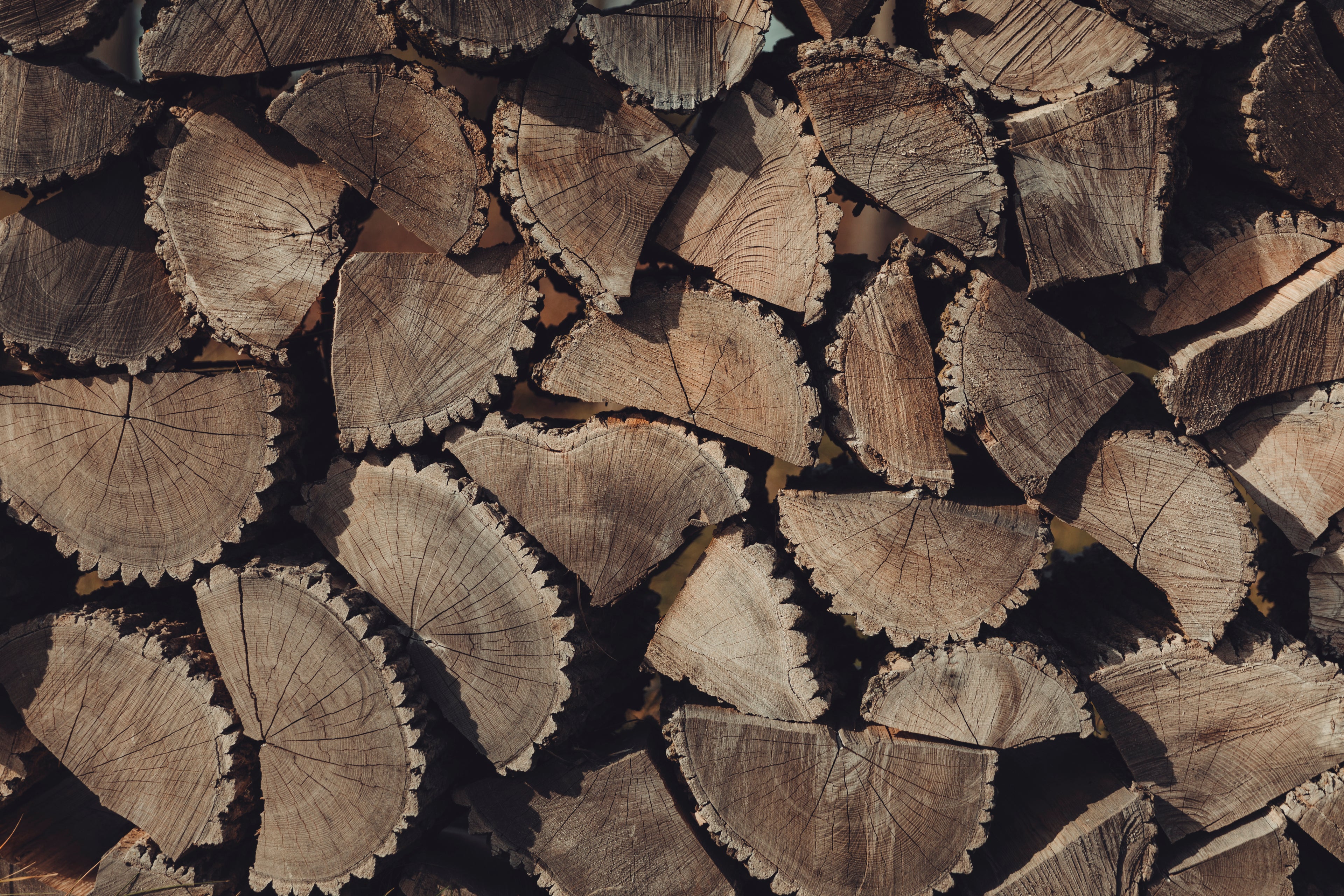
Reclaimed pitch pine flooring specialists based in Harrogate
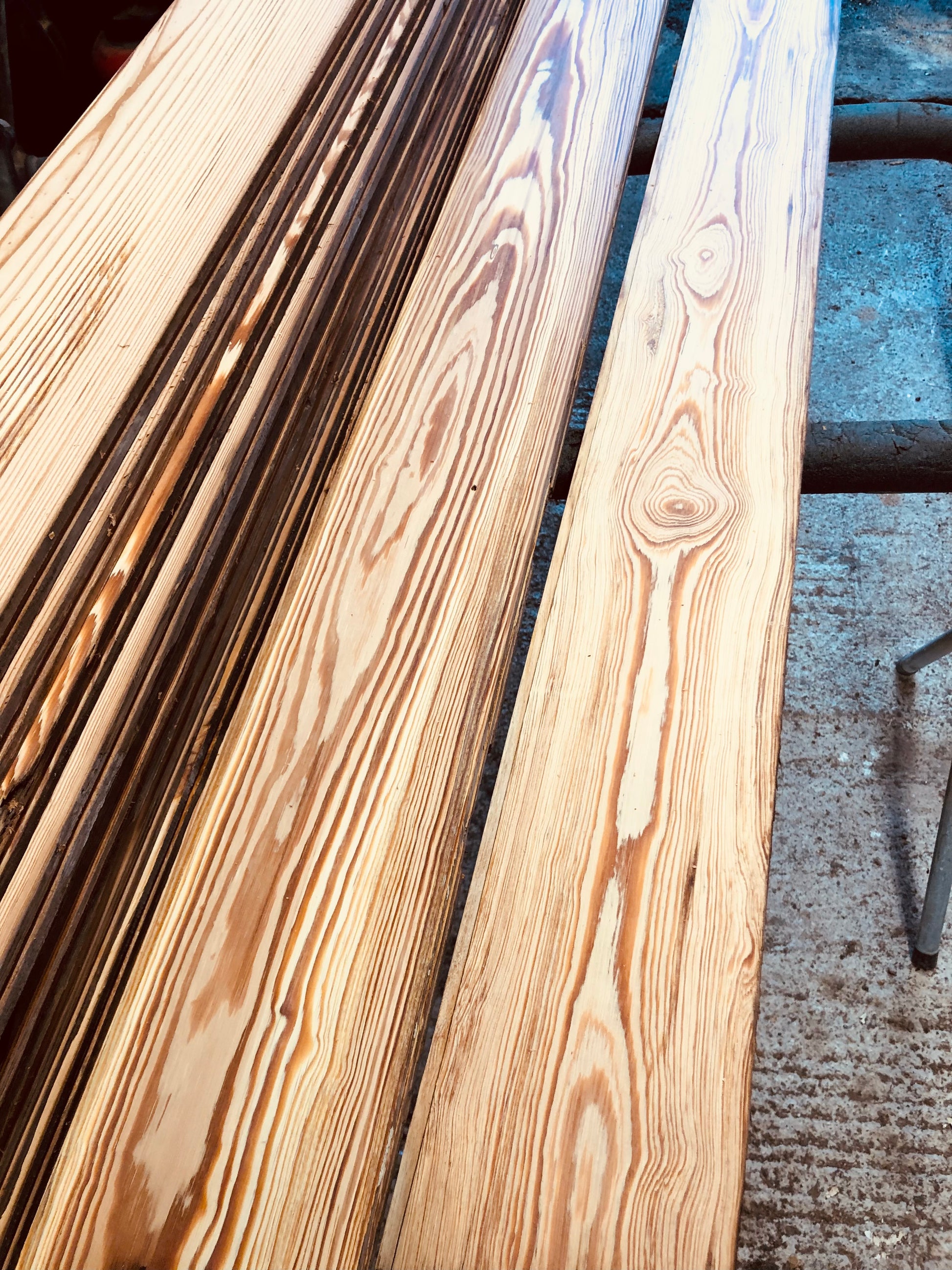
Harrogate Flooring
Solid Pitch Pine Floorboards
Share
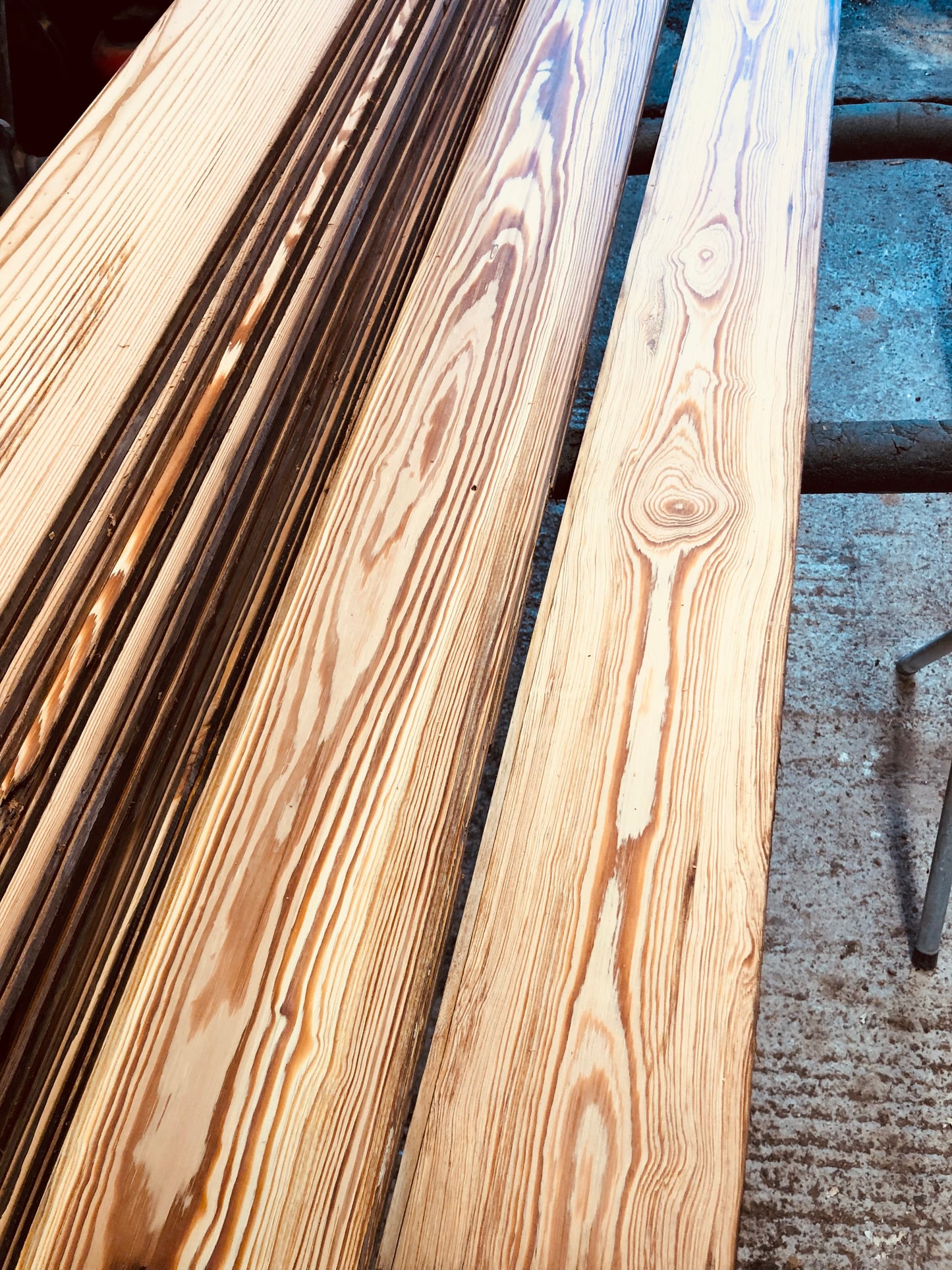
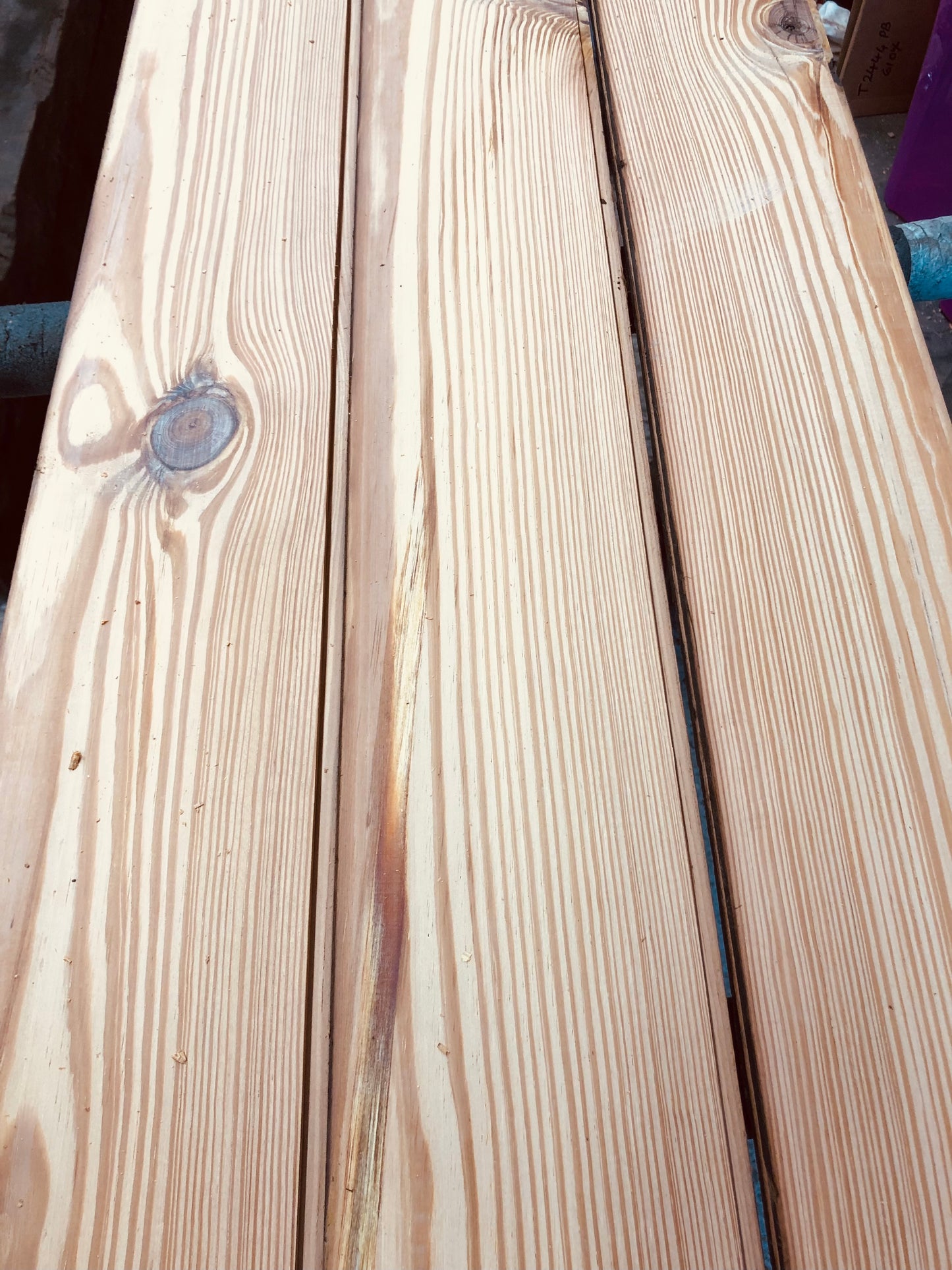
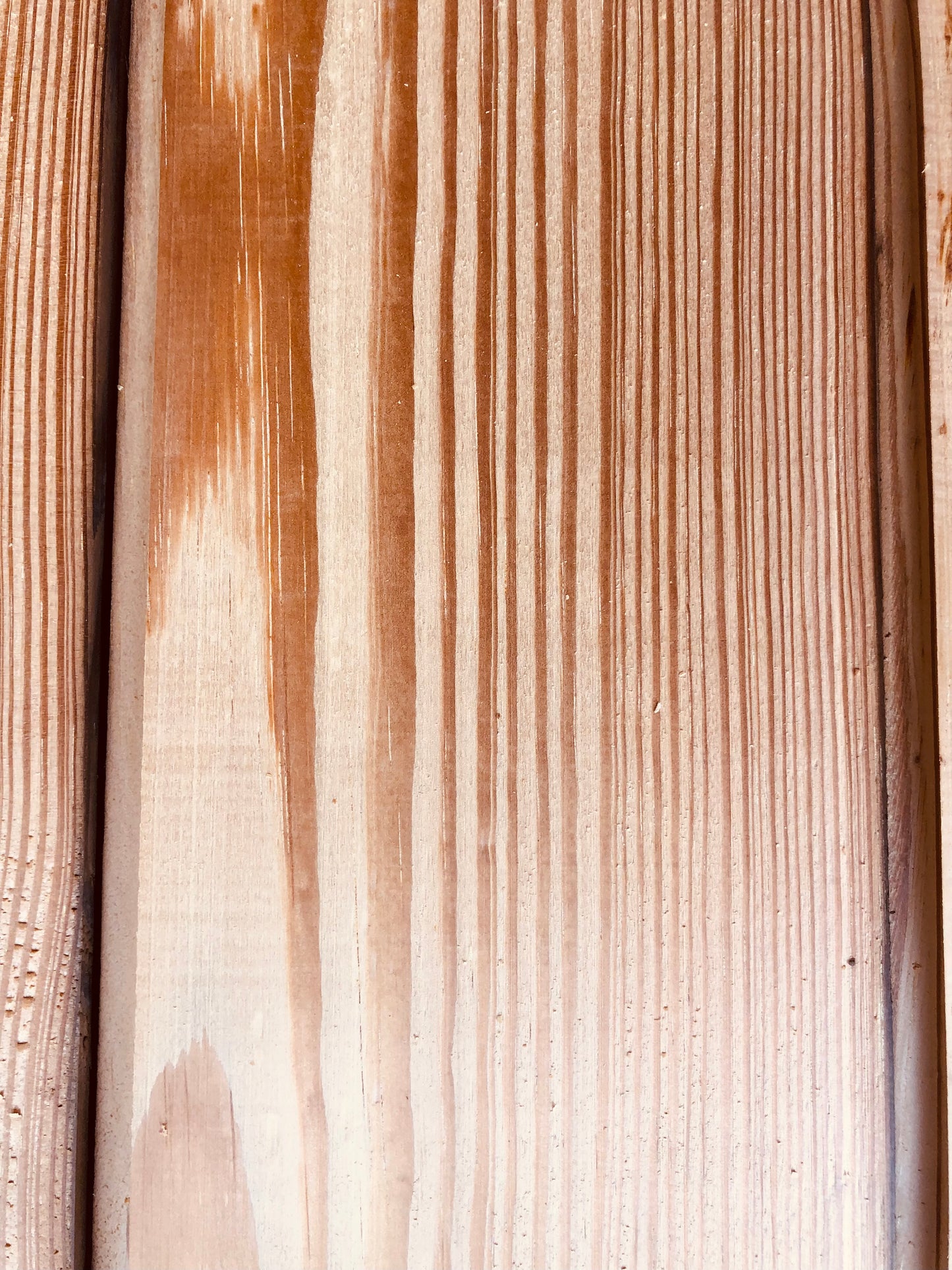
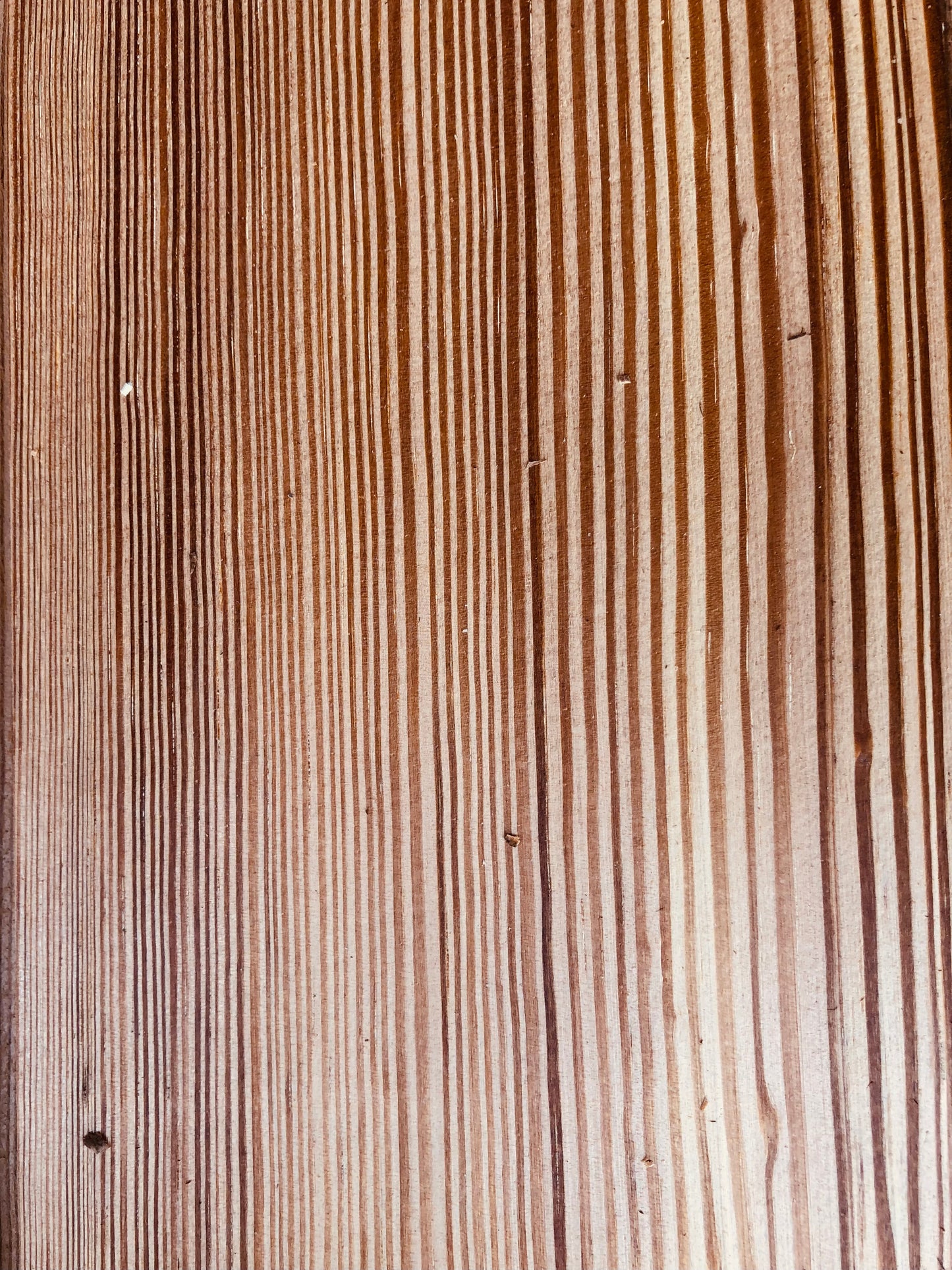
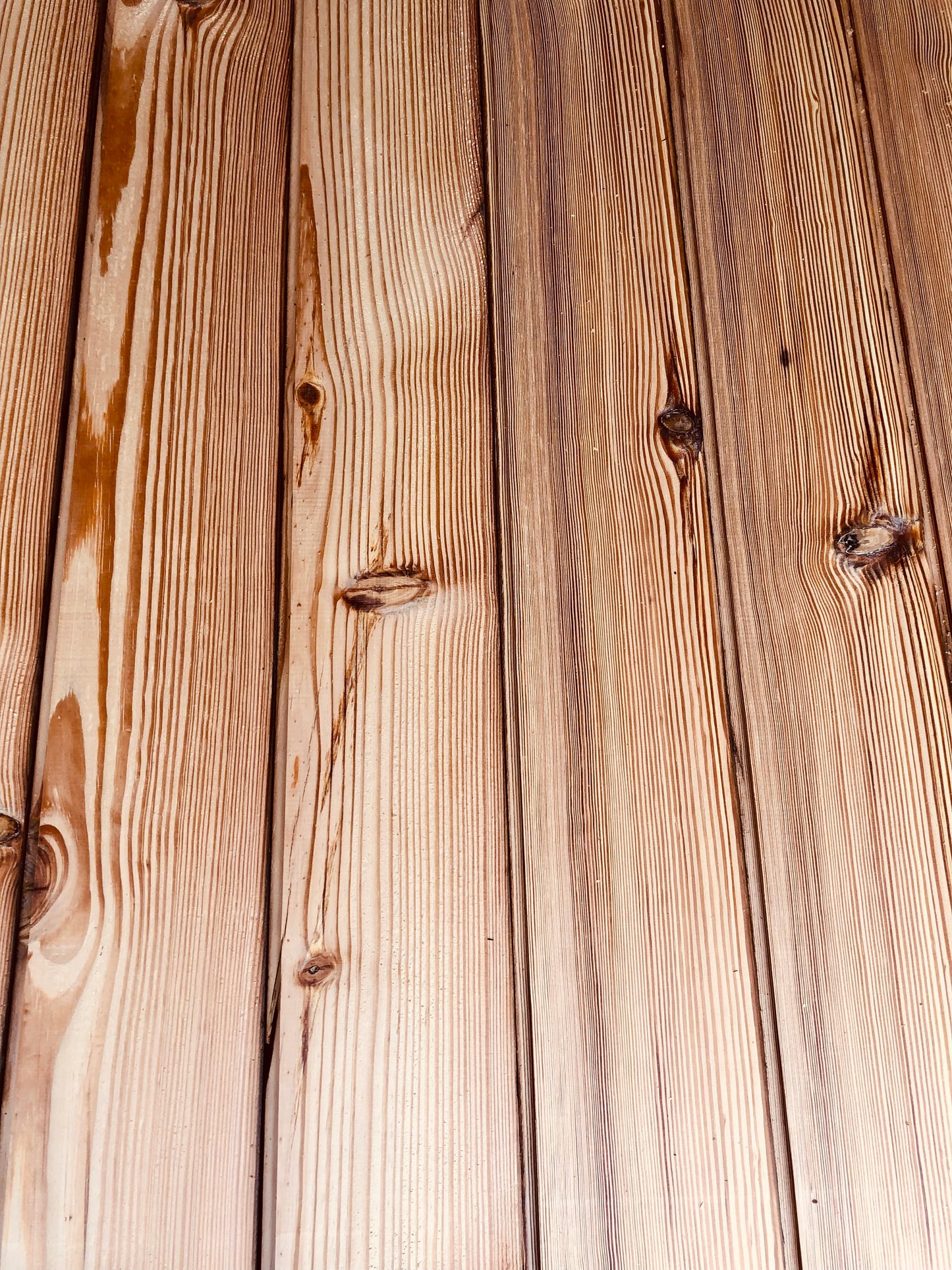
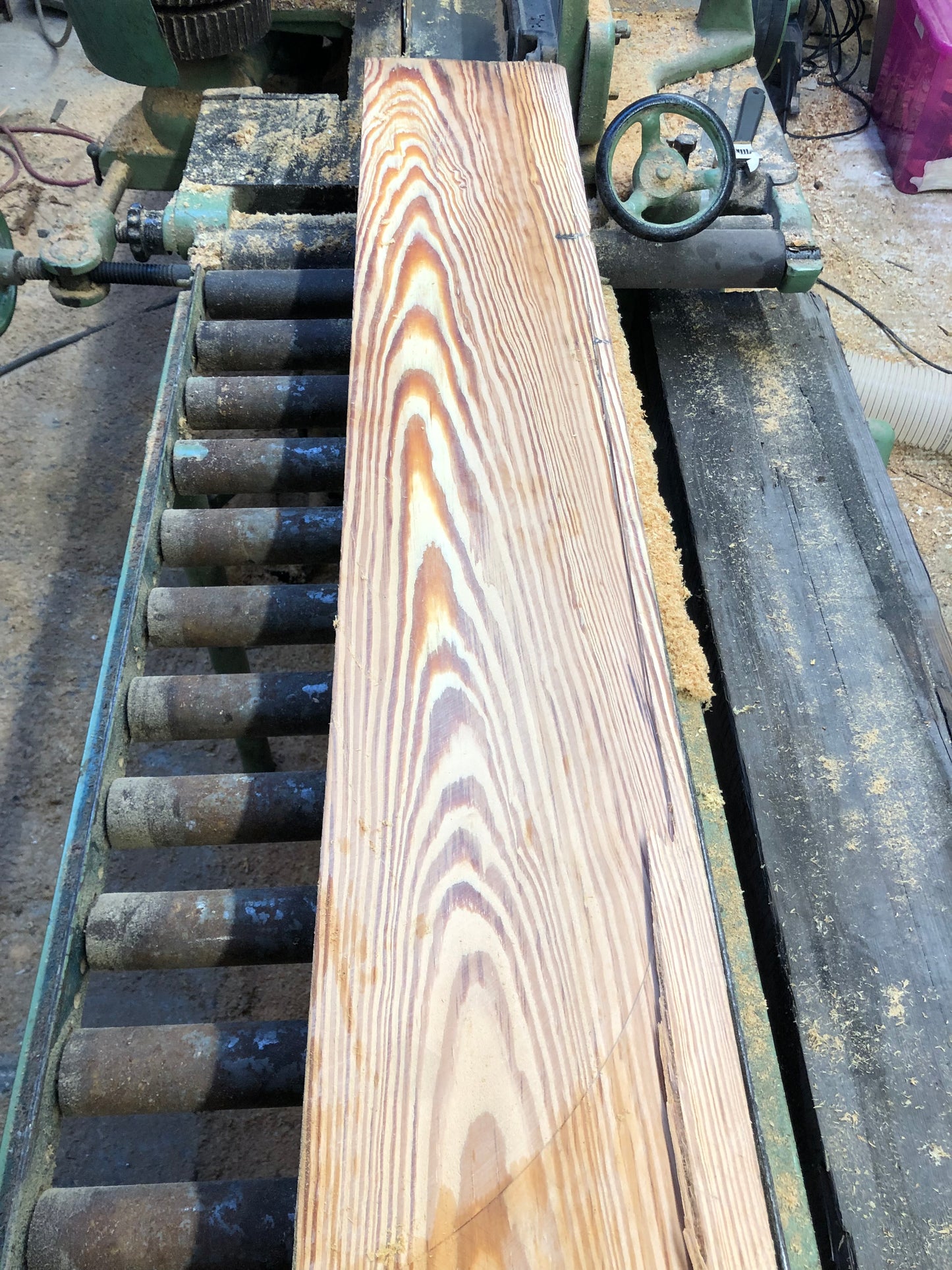
Our Process
All our flooring is made in our Harrogate workshop using reclaimed pitch pine beams. If you’re interested in how our floorboards are manufactured, take a look at the various processing stages below.
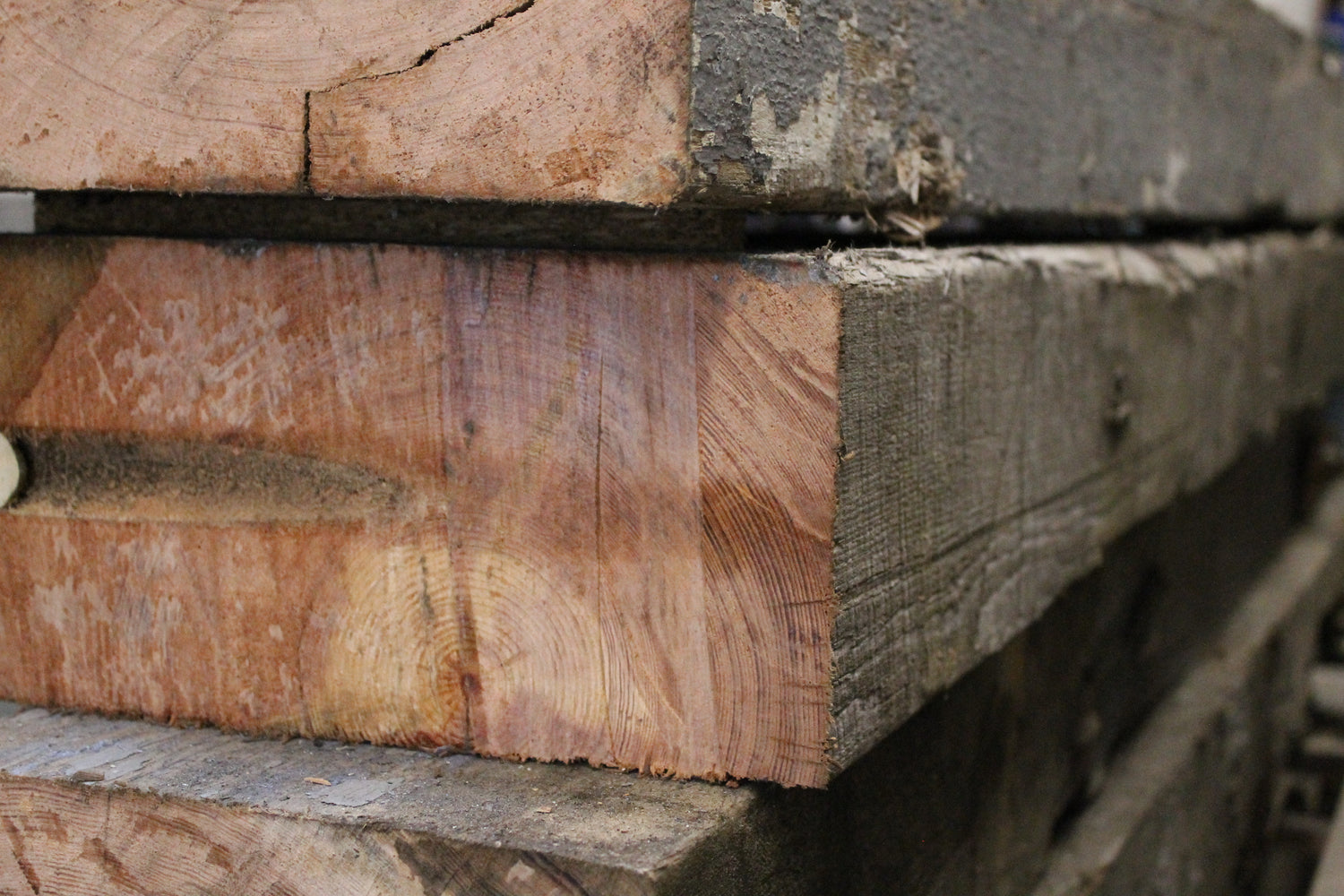
Choose Timbers
The first part of the journey is selecting the right timbers to work with. They need to be solid and rot-free with minimal twist.
All the beams are reclaimed from old mills and factories so have plenty of character and have thoroughly dried out on the inside. We dry-store the timbers in our workshop ahead of processing.
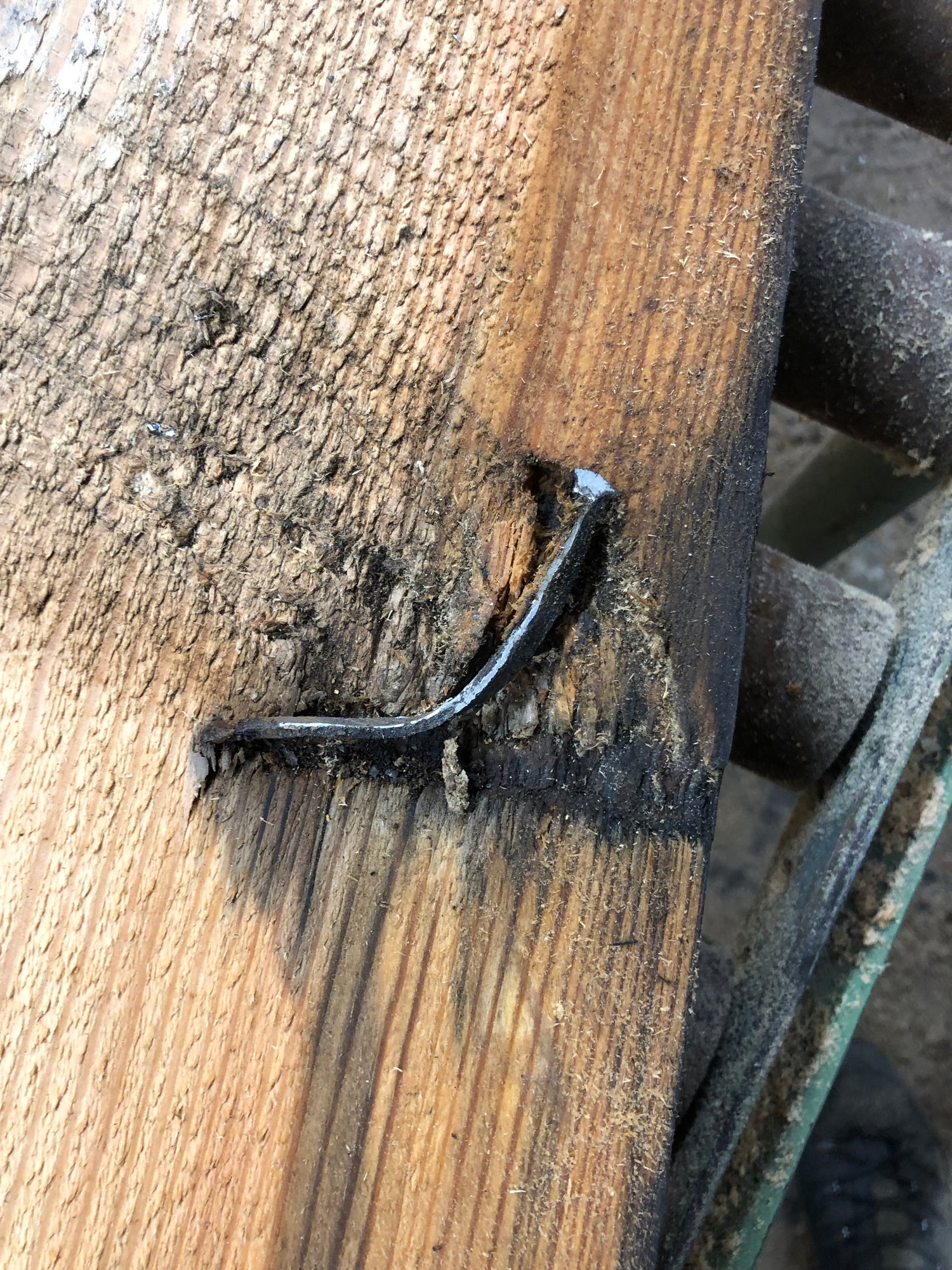
Remove Metal Objects
Removal of foreign objects is a very important part of the process.
Screws, nails, wire and bolts are the most common objects we have to remove and some are buried deep within the beams so a metal detector is a must!
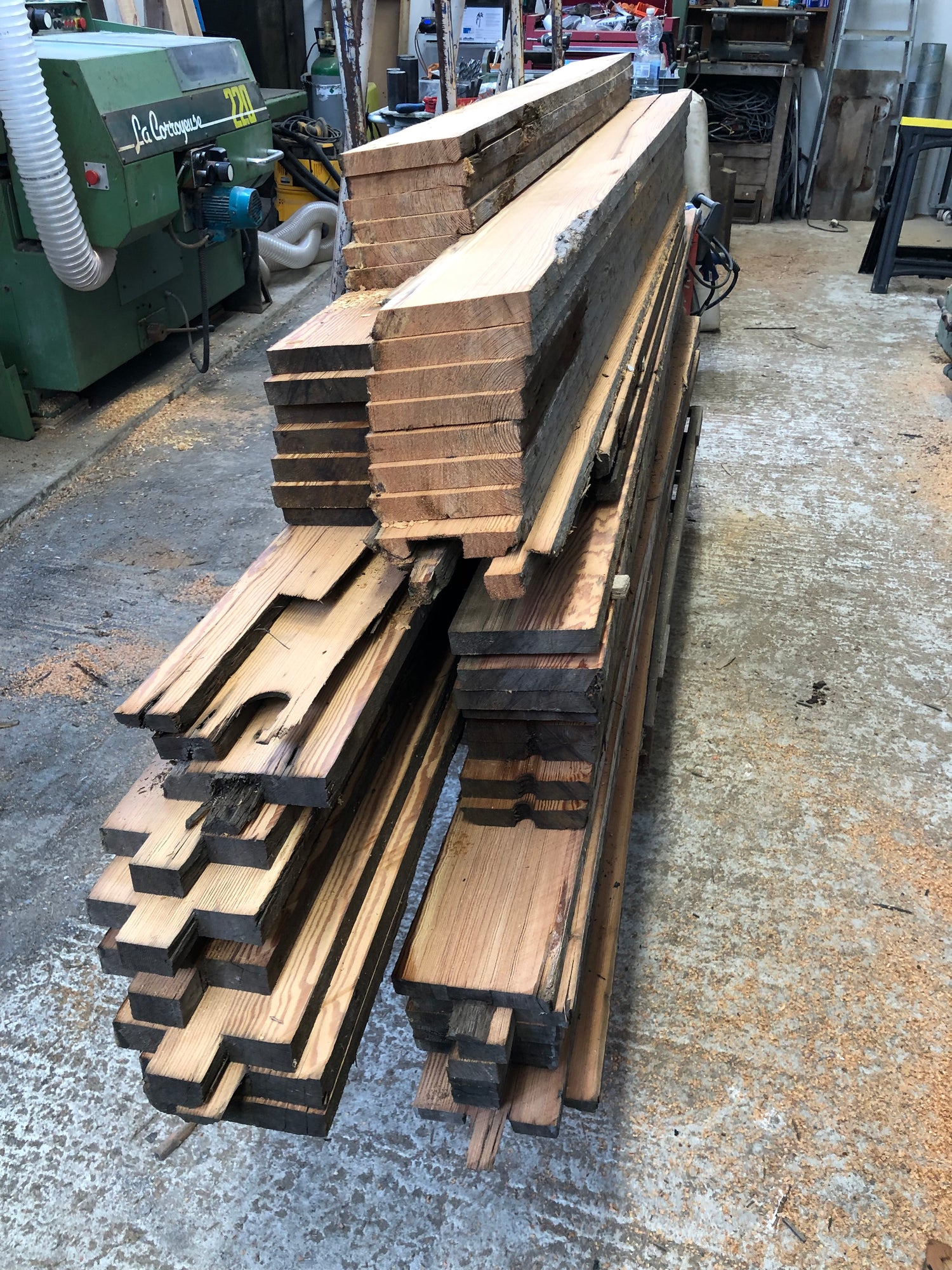
Resaw into Planks
When the timber is clean of metal, it is ready to be resawn into thin planks, slightly oversized to the finished floorboard dimensions.
This is where the grain and figuring of the wood is exposed for the first time in hundreds of years and the pitch pine releases its distinctive scent!
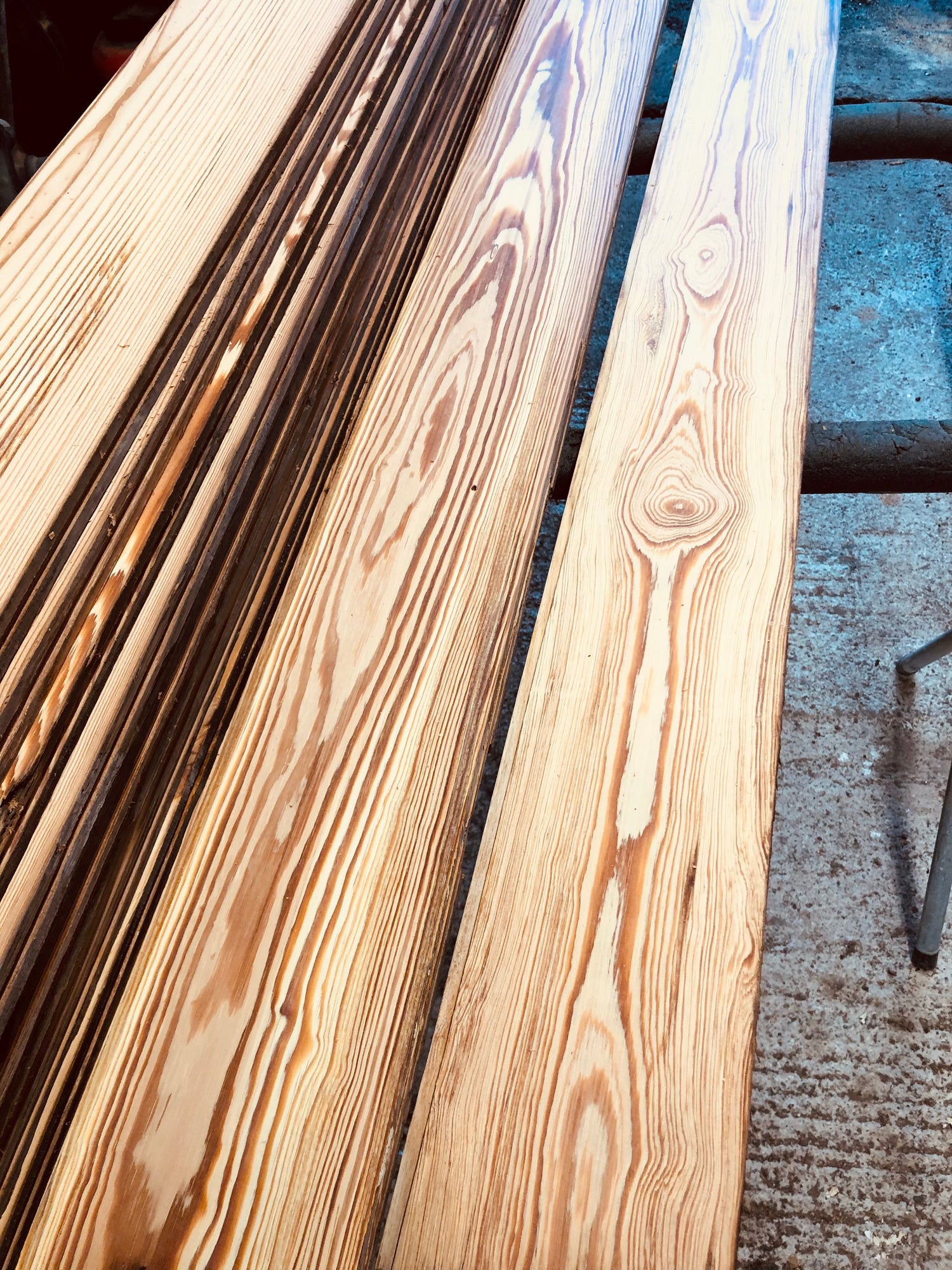
Plane and Profile Boards
The planks are now fed into the 4-sided planer moulder. If we’re making tongue and groove flooring, the machine planes the top and bottom of the boards square, and adds a tongue down one edge and a groove down the other. For straight edge flooring, the machine planes all four sides square.
Rejects are discarded at this point if they don’t make the grade.

Prepare Delivery
Flooring is stacked up onto racking ready for collection or delivery.
Your order status will be updated and an email confirmation sent out.
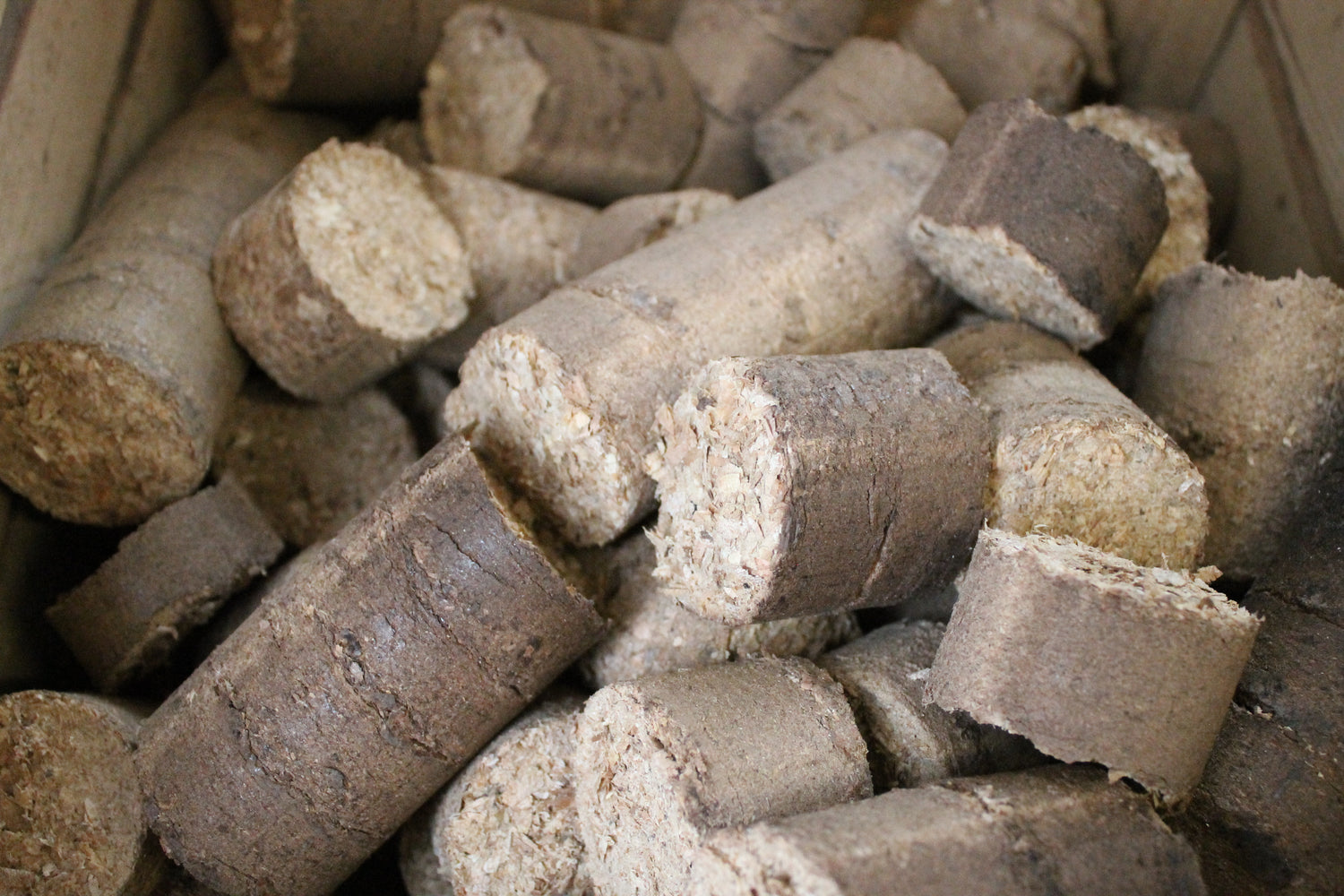
Process the Sawdust!
As you can imagine, all this processing produces a lot of sawdust. We have two large dust extractor units which remove all the sawdust and chips from the machines during processing.
We then feed the sawdust and chips into a briquette press so that our waste is turned into a usable fuel, which we either sell or burn to heat our workshop!
Recent Posts
-
A little insight into how we make our tongue an...
Setting the cutter block tooling used to apply tongue and groove edging.
A little insight into how we make our tongue an...
Setting the cutter block tooling used to apply tongue and groove edging.
-
-